In the pulp and paper industry, black liquor, a byproduct of the kraft process, is concentrated through evaporation in the recovery line. Once efficiently evaporated, this black liquor is burned for energy. During this process, steam is generated, which can then be used to power the mill or for other processes within the facility. This steam generation is crucial for efficient operations and the self-sufficiency of pulp mills, while also improving their sustainability.
Fouling in the recovery line is one crucial issue that impacts this process and disturbs efficient steam generation. It reduces heat transfer efficiency and decreases generation capacity. This in turn leads to an increased need for extra steam to keep the black liquor evaporation process on-going, as the steam generated within the process might not be enough. This creates extra costs and lowers operational sustainability. Fouling also requires frequent maintenance, often meaning process downtime.
This article will discuss steam generation in the recovery line, focusing on the negative effects of fouling and providing an efficient solution. We’ll also showcase real-life results achieved by using Altum’s ultrasound solution for fouling prevention.
Critical Role of Efficient Steam Generation in the Recovery Line
The black liquor recovery process represents a critical energy nexus within modern pulp mills, transforming what was once considered waste into valuable thermal energy. Through efficient evaporation and combustion, concentrated black liquor becomes a significant energy source. This process also involves the recovery of valuable process chemicals.
This closed-loop process demonstrates industrial sustainability, where steam both drives the concentration process and becomes its valuable output. The recovery line’s ability to maximize energy generation while minimizing fresh steam consumption directly impacts overall mill efficiency. This creates a compelling economic and environmental incentive to maintain optimal performance.
The recovery boiler’s steam generation efficiency fundamentally affects pulp mill economics:
- Net energy production depends on maximizing steam output per unit of black liquor solids
- Process stability requires consistent steam generation despite varying black liquor properties
- Electricity generation potential (through turbines) depends on steam temperature and pressure
- Mill expansion capacity often hinges on optimizing existing recovery boiler performance
Within this system, even minor efficiency improvements create cascading benefits through reduced purchased energy, increased electricity production, and improved chemical recovery rates. Reversed, decreased efficiency, such as caused by fouling, negatively impact the whole process.
Fouling Challenges in the Recovery Line
The black liquor recovery process creates uniquely challenging fouling conditions: the equipment operates continuously at high temperatures with chemically complex fluids, creating ideal conditions for buildup formation and efficiency losses.
A key issue is fouling in evaporators, as the efficiency with which evaporators can evaporate water directly affects the maximum amount of steam they are able to generate. Heaters and concentrators are also an important part of the evaporation process: by integrating heaters and concentrators, the evaporation process becomes more efficient, leading to better steam economy and reduced operational issues. Fouling negatively impacts heat transfer, which affects the efficiency of all process components. Based on literature and customer cases, fouling typically reduces the overall efficiency of a black liquor evaporator by 10-15%, often even more.
Fouling creates measurable negative effects on operations:
- Energy efficiency losses: equipment require more steam to evaporate the same amount of water
- Production capacity limitations
- Increased maintenance requirements: frequent cleaning, e.g., weekly or daily boil-outs.
- Equipment lifespan reduction
- Steam pressure and temperature inconsistencies
These in turn effect the costs of the operation and impact profitability. For example, as energy efficiency decreases, energy costs often increase as the mill needs to use outside energy sources. Beyond direct energy impacts, fouling-related capacity constraints often force increased dependency on auxiliary boilers, adding thousands to daily operating costs during peak production periods. Maintenance is also another expense, especially if it requires special chemicals or the use of cleaning robots. Fouling, in addition to intense and frequent maintenance, cause equipment to wear out faster, which is neither economical nor sustainable.
Fouling Management Strategies
Current Management Approaches
Traditional cleaning approaches include chemical treatments using acids, alkaline solutions, and chelating agents to dissolve buildup, and mechanical interventions such as high-pressure water jetting, scraping, and abrasive blasting. Recirculating or boiling out with condensate or weak liquor is also applied during operation.
Despite their effectiveness, these methods are fundamentally reactive rather than preventive. System efficiency degrades progressively between cleanings, which means elevated energy consumption and reduced steam output during normal operation. The reactive approach requires planned or unplanned downtime affecting production, often results in higher long-term costs, and creates unpredictable maintenance scheduling challenges. These limitations have driven interest in more preventive fouling management strategies.
Preventive Solution: Ultrasonic Fouling Prevention
To combat challenges related to fouling in the recovery line and steam generation, forward-thinking mills are now implementing ultrasonic technology that prevents fouling formation within these critical systems. Preventive fouling management maintains peak energy recovery without production interruptions or chemical interventions.
Altum’s ZPD (Zero Process Downtime) Ultrasound solution provides a chemical-free, efficient clean-in-place system for fouling removal and prevention. It is externally applied, so the process doesn’t need to be stopped, or equipment disassembled. This ultrasound technology eliminates the need for harsh chemicals and can be precisely controlled with innovative software. We are the only company in the world that can combine high power capacity with ultrasound control.
Altum’s high-power ultrasound prevents fouling in evaporators, heaters or concentrators, often calcium-based, by inducing a crystallization effect. By sonicating black liquor before it goes through the heated elements in the equipment, ultrasound can induce nucleation and create a controlled crystallization effect so that the black liquor will not adhere to heated surfaces as scale. See picture below for visual explanation.
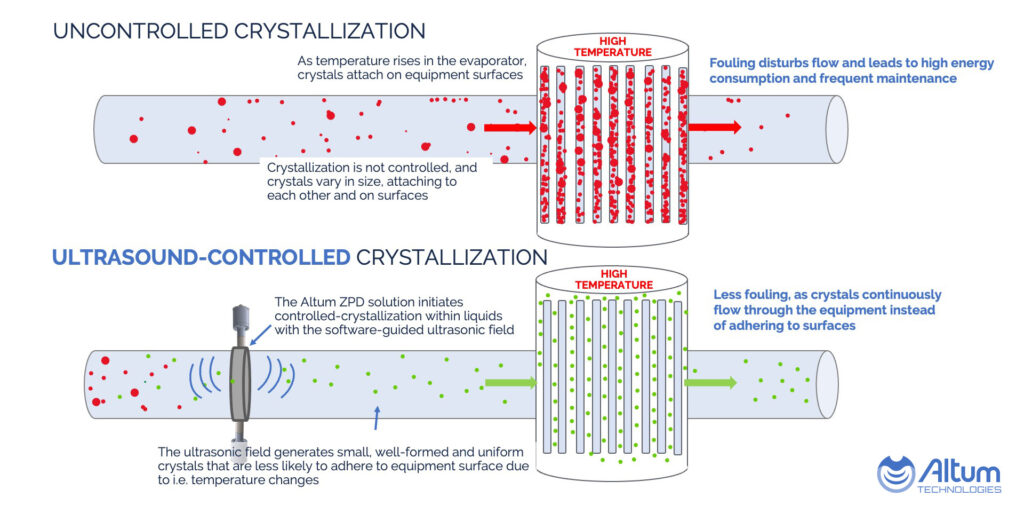
Case Examples: Real-World Impact
Fouling prevention in a black liquor evaporator
A Mitsubishi Paper mill had been experiencing issues with scaling in black liquor evaporators, mainly caused by calcium carbonate. Due to these scaling issues, it became difficult to maintain the process, especially for the intended four-month period during the winter. In the worst case, the process had to be stopped every month for a cleaning break.
Fouling increases the temperature difference between the heating steam and black liquor by decreasing heat transfer efficiency. If this difference exceeds 20°C, the operation is shut down for cleaning. Before ultrasonic treatment, the temperature difference reached 20°C within a month. With ultrasonic fouling prevention, it remained stable for four months, reducing steam usage by over 80 tons. Read more about fouling prevention at a Mitsubishi Paper mill.
Fouling prevention in a black liquor heater
In this case, there were fouling issues in a black liquor heater. Fouling disrupted the black liquor evaporation process and led to decrease in production efficiency and output, as well as increase in energy consumption. As fouling increased, more steam was required to be fed into the pipe to maintain production efficiency, resulting in a higher energy demand.
After implementing Altum’s solution, the steam valve opening degree remained below 80% during sonication for over 8 weeks, meaning no extra steam was required to maintain original production efficiency – without sonication the opening degree reached 100% in 4 weeks. This meant savings of 30 million MJ in extra energy per year. Read more about preventing fouling in a black liquor heater.
Fouling prevention in a black liquor concentrator
In another case, fouling led to decreased production efficiency, increased steam consumption, and higher process pressure. The primary fouling issues were in the concentrator, located after the evaporators. Fouling led to a boil-out frequency of every 7 to 10 days.
By efficiently preventing fouling, Altum helped the company decrease boil-outs by 80%. By decreasing the number of boil-outs, the mill also achieved a 67% decrease in steam usage.
Interested to learn how Altum’s ultrasound solution can help improve your recovery line? Contact our experts for more information.