Biogas plants are critical assets in our transition to sustainable power generation. However, these systems face unique maintenance challenges that traditional cleaning methods alone cannot efficiently address. At Altum Technologies, we understand that modern biogas facilities require innovative maintenance approaches to maximize efficiency, extend equipment lifespan, and ensure optimal performance.
Current Issues in Biogas Plant Maintenance
Biogas plants convert organic waste into valuable energy through anaerobic digestion, but this biological process creates persistent maintenance challenges. Anaerobic environments can create ideal conditions for fouling, particularly struvite formation, which is one of the most common scaling challenges in these processes. Struvite, magnesium ammonium phosphate (often referred to as MAP), forms in environments where ammonia, magnesium, and phosphate concentrations are high, with alkaline pH levels. Biogas manufacturing processes typically process organic waste materials containing high levels of nitrogen (in the form of ammonium), magnesium, and phosphate. The anaerobic conditions often lead to an increase in pH levels, creating alkaline conditions and turning these substances into struvite.
Fouling, whether caused by struvite, other phosphates or minerals, or even biofilm, causes significant issues in biogas production processes. These include:
- Reduced Heat Exchanger Efficiency: Reduced thermal transfer due to progressive contamination
- Weakened Digester Performance: Suboptimal mixing and reduced biological activity from sludge buildup
- Pipeline Restrictions: Flow limitations and pressure drops from progressive clogging
Traditional maintenance approaches—typically involving chemical cleaning, mechanical scrubbing, or complete system shutdowns—are increasingly recognized as insufficient, environmentally problematic, and economically unsustainable. Combatting fouling can even require daily cleaning breaks, which lead to downtime, mechanical labor, and high water and chemical use. In addition, the problems get progressively worse between cleanings and the process does not run at optimal efficiency: this means losses in production, higher energy costs, and increased strain on equipment. For example, pushing liquids through a clogged pipe takes up a lot more energy and puts a lot more pressure on the pipe structures.
The Business Case for Modern Maintenance
As mentioned above, fouling negatively impacts operational efficiency and directly impacts the cost efficiency of production. So why not look for a change? By moving from traditional and reactive maintenance to more modern solutions that adapt to the process, biogas producers can achieve multiple benefits.
Investing in advanced biogas plant maintenance technologies delivers compelling returns:
- Increased Biogas Production: higher output from well-maintained systems, without unnecessary production breaks
- Extended Equipment Lifespan: longer operational life for critical components, with less tear and wear caused by fouling
- Reduced Maintenance Costs: moving from daily or weekly maintenance breaks to none at all can significantly lower maintenance costs, depending on the cleaning methods previously used.
- Enhanced Sustainability Profile: Minimal chemical use and waste generation
- Improved Safety: Reduced need for confined space entry and hazardous manual cleaning
One easy way to achieve these benefits is to use high-power and externally applied ultrasound to prevent fouling.
Non-Invasive Ultrasound Fouling Prevention Technology
Among the most promising advancements in modern maintenance is non-invasive ultrasonic clean-in-place system. This revolutionary approach uses sound waves to prevent fouling and remove existing buildup without process downtime or chemical use.
Here at Altum Technologies, we utilize ultrasound technology to prevent fouling formation and remove existing buildup by affecting liquids and bonds and inducing microvibrations. What distinguishes this technology from other ultrasonic cleaning systems are two key advantages: precise ultrasound control capabilities and non-invasive external application that requires no process modifications, like welding, and enables constant prevention. The system combines powerful ultrasonic output with software that directs the ultrasound exactly where needed. With remote monitoring done by Altum’s experts, customers benefit from optimal performance with minimal operational involvement.
Key Benefits Include:
- Zero Production Interruption: Prevention or cleaning occurs while systems remain operational, eliminating costly downtime that traditional cleaning methods require. This continuous maintenance approach ensures biogas production continues uninterrupted, increasing annual output and revenue.
- Chemical-Free Process: Environmentally responsible maintenance without harsh cleaning agents reduces environmental impact and eliminates chemical handling risks. This approach aligns with strict environmental regulations while protecting operator safety.
- Targeted Treatment: Precision cleaning focuses on problem areas without disturbing the entire system. Advanced controlling and guiding capabilities allow directing ultrasonic power exactly where needed, optimizing cleaning efficiency.
- Preservation of Equipment Integrity: Non-abrasive technology extends component lifespans by eliminating the surface damage caused by mechanical cleaning methods or corrosive chemicals.
- Adaptability to Various Deposit Types: The technology effectively addresses multiple fouling challenges common in biogas plants, including struvite crystallization, calcium carbonate scaling, biofilm formation, and organic matter accumulation.
Results achieved
Struvite fouling posed a challenge for our customer Ductor, which encountered fouling across various stages of its process. Due to the struvite fouling in the pipelines, plate and frame heat exchangers and pumps, cleaning had to be performed every one to two days and was done with CIP (Clean-in-place) using citric acid and high-pressure wash. This in turn led to production downtime, manual labor, and the handling of chemicals.
By preventing fouling with Altum’s solution, the customer has been able to reduce process downtime associated with cleaning from 2 hours per day to just 2 hours per month. On top of this, the process has become much more stable, and the biogas production and biological fertilizer recovery processes have been improved.
Overall, with Altum’s solution:
- Decrease in operation downtime, from 2 hours/day to 2 hours/month.
- 6 tons decrease in citric acid use per year.
- Reduced CO2 emissions.
- An improved and stable production and recovery process.
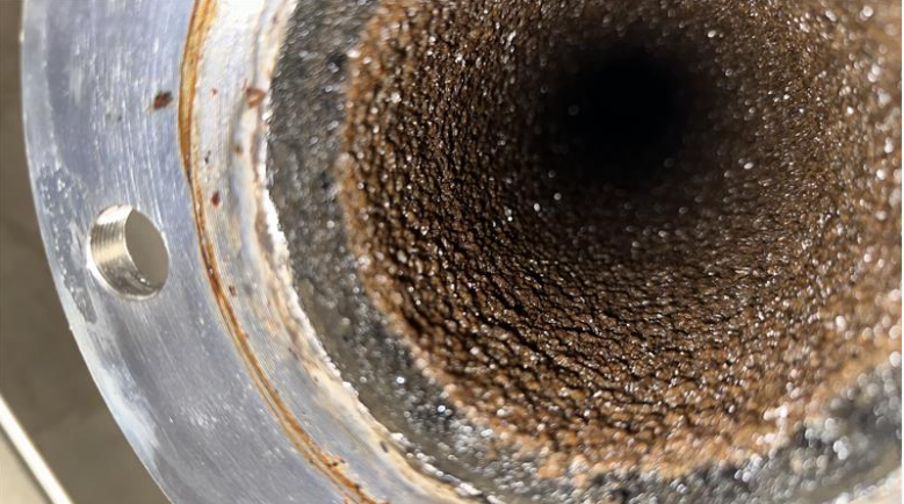
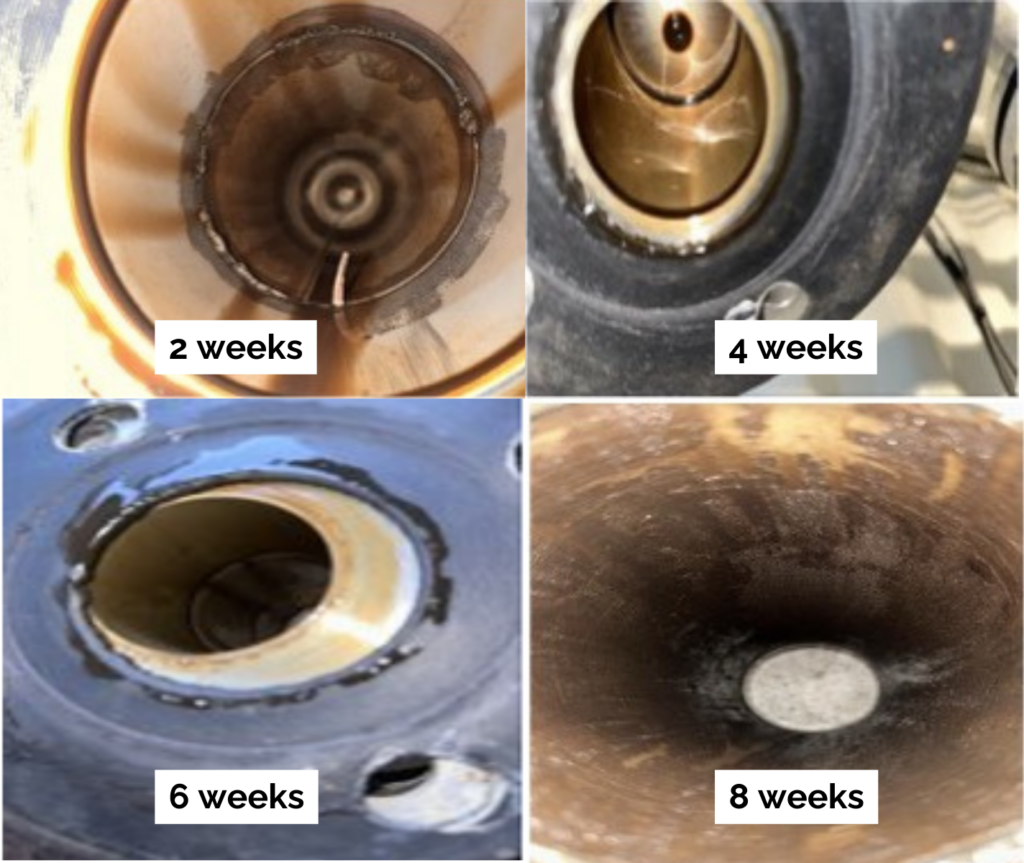
Before: thick buildup of struvite (10 mm) on pipes. After: very minimal buildup after 8 weeks of production.
The future of biogas plant maintenance lies beyond traditional cleaning approaches. By utilizing technologies like Altum’s non-invasive ultrasound fouling prevention solutions, biogas plant operators can achieve new levels of efficiency, sustainability, and profitability.
Want to discuss how we could improve your biogas process? Contact our experts for further information
Follow us on LinkedIn so you won’t miss our future news and insights.