Traditionally, fouling management in industrial processes has relied heavily on reactive maintenance. This approach involves addressing fouling issues only after they have become significant enough to impact operations. Common methods include mechanical cleaning and chemical treatments, which often require periodic shutdowns for maintenance. While these methods can be effective in the short term, they often lead to frequent interruptions and increased operational costs.
However, there are alternatives to reactive fouling management. Preventive maintenance strategies focus on preventing fouling before it occurs, rather than reacting to it after the fact. Techniques such as high-power ultrasound, chemicals, and advanced filtration systems are employed to keep equipment clean and functioning optimally. By preventing fouling, companies can in most cases reduce downtime, lower maintenance costs, and improve overall efficiency.
This blog post will discuss fouling, its impact on process efficiency, and the challenges related to traditional reactive maintenance, and showcases how preventive fouling management can improve operations across industries.
Understanding Fouling Mechanisms
Most industrial processes struggle with fouling to some extent. Fouling is caused by a variety of substances, depending on the process. Common types include:
- Carbonates, such as potassium, sodium and calcium. For example, calcium carbonate fouling is especially common in black liquor evaporation processes.
- Sulfates, such as calcium, nickel, or lithium sulfate. These can often be an issue in minerals processing.
- Biofilm, a slimy layer of microorganisms. Biofilm fouling is often a concern in the pulp and paper industry, especially when seawater is employed for cooling purposes in industrial equipment.
- Oxides, such as rust (iron oxide). Because of the way rust forms (when iron reacts with oxygen in the presence of water), iron oxides can become a big issue in heated pipelines especially as pressure increases.
- Phosphate minerals, such as struvite (magnesium ammonium phosphate). Struvite poses a significant challenge in wastewater and sewage treatment as well as biogas production due to the anaerobic conditions used in these processes, which release ammonium and phosphate from waste materials.
You can read more about fouling types here.
Fouling is often an issue in areas with high temperatures and/or temperature fluctuations, such as heat exhanger or evaporator tubes and lamellas, and pipes transferring process liquids. These equipment are also prone to clogging due to fouling, which disturbs the whole process flow. Buildup on equipment surfaces also disturbs heat transfer efficiency and can also lead to quality issues in the end product.
With traditional reactive maintenance, the effects of fouling often require cleaning stops on a weekly or even daily basis. This cleaning can involve mechanical methods like hydroblasting or cleaning robots, chemical treatments to remove the fouling, or boilouts. This in turn leads to production breaks and profit losses.
The True Cost of Reactive Cleaning
Reactive maintenance can be costly for several reasons. First, unplanned shutdowns disrupt production schedules and lead to lost revenue and decreased efficiency. Second, the labor and materials required for cleaning and repairs can be very expensive, especially if they are required often. Fouling and frequent cleaning also contribute to equipment wear and tear, and repairs can be a significant expense. Additionally, the energy efficiency of equipment decreases as fouling builds up, resulting in higher energy consumption and increased operational costs. Over time, these expenses can accumulate and significantly impact the bottom line.
Another aspect is sustainability. High energy consumption caused by fouling leads to high CO2 emissions, in addition to the environmental impact of chemicals and/or the large amounts of water needed for cleaning activities. In addition to being harmful to the environment, these emissions can also be a big expense depending on the carbon credit system in place in the area. In many areas, there are also regulations and sanctions in place for e.g., water pollution, which can be a big risk when using harsh and dangerous chemicals.
The Preventive Approach
Luckily, there is an alternative to reactive maintenance. By utilizing preventive fouling management companies can save in costs, improve overall efficiency and in most cases, improve sustainability. The goals for fouling prevention can differ based on the process: for example, the goal can be to get rid of frequent cleaning breaks altogether, or to get rid of certain cleaning tactics like chemicals or mechnical cleaning.
One fouling prevention method is pre-treatment, which involves removing potential foulants from the feed water or other fluids to protect the equipment. These techniques include, for example, filtration, screening, sedimentation and oil and grease management. Another more traditional fouling prevention method is chemical treatment, which means adding chemicals like anti-scalants, biocides, and dispersants to prevent fouling from attaching on equipment surfaces.
One highly efficient fouling prevention method that is chemical-free and does not require any changes to the existing process is ultrasound. By utilizing the qualities of ultrasound, such as the ability to induce cavitation, microscopic vibrations, or sonocrystallization, fouling can be prevented altogether.
Altum Technologies’ High-Power Ultrasound
Altum specializes in high-power ultrasound for fouling prevention and removal. What sets it apart from other ultrasound technologies is its ability to control the ultrasound with software and focus ultrasound power precisely where it is needed. In addition, it allows for fouling prevention or removal without interrupting or altering the production process. It is externally applied on the equipment without welding, which makes it a very versatile solution: Altum’s ultrasound solution can be applied to various processes and equipment, including pipes, evaporators, and pumps.
Benefits of Preventive Fouling Management with Ultrasound
- Chemical-Free Solution: Altum’s ultrasound technology prevents and removes fouling without the need for chemicals, making it an environmentally friendly option.
- Increased Efficiency: The technology improves process efficiency by maintaining clean surfaces, which enhances heat transfer and pumping efficiency.
- Reduced Downtime: By preventing fouling, Altum’s solution minimizes unplanned interruptions and maintenance, leading to increased uptime and productivity.
- Extended Equipment Lifespan: The reduction in fouling also decreases wear and tear on equipment, extending its operational life.
- Cost Savings: No need for expensive cleaning methods, like cleaning robots. No lost production, no profit losses.
- Increased Sustainability: In addition to being chemical-free, due to reduction in maintenance requirements, such as hydroblasting, Altum’s solution helps save water. By improving efficiency, it can also significantly reduce energy consumption and CO2 emissions.
Case Examples
We have achieved great results across industries by efficiently preventing fouling. For example, at Mitsubishi Paper fouling prevention in evaporators led to a 300% increase in operation cycle length, from one month to four months without cleaning breaks. They were also able to get rid of the acid they previously used for fouling mitigation.
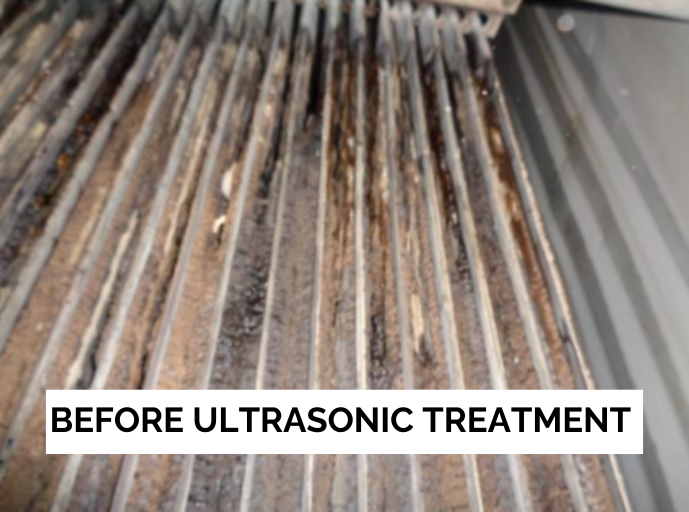
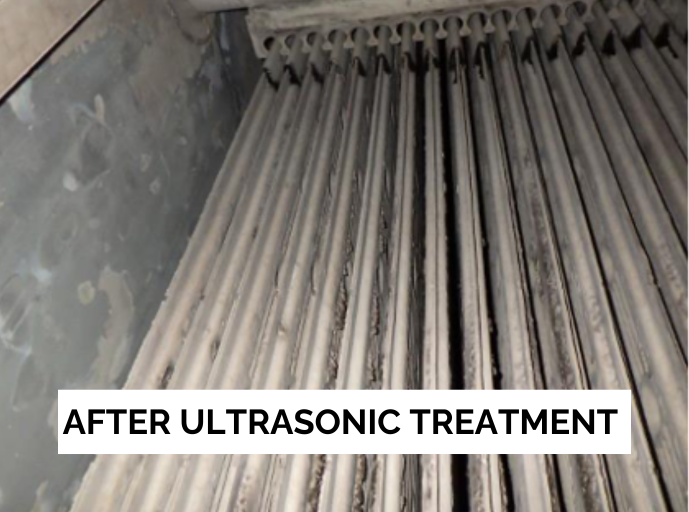
Another example from the Pulp and Paper industry is from preventing fouling in a black liquor heater. In this case, we were able to improve flow rate by 5% and the mill no longer needed to use extra energy to maintain production efficiency: this led to energy savings of 30 million MJ per year.
In a minerals processing facility, fouling prevention with Altum’s ultrasound led to a 100% increase in production cycle duration: this meant 35 days more uptime per year.
Want to find out how you can reach similar results with preventive fouling management while making your process more sustainable and environmentally friendly? Don’t hesitate to contact our experts for more information on fouling prevention with Altum’s innovative ultrasound.
Follow us on LinkedIn to stay tuned for our future news and insights.