Evaporators are crucial in the pulp and paper industry for concentrating black liquor, a byproduct of the kraft pulp process, by removing water and increasing its solids content. Mills can then burn this concentrated black liquor in the recovery boiler to generate steam and power, making it possible for the process to be self-sufficient regarding energy. However, fouling in black liquor evaporator tubes and lamellas is a widespread issue. Fouling causes blockages, reduces heat transfer and evaporation efficiency, and requires frequent stops for cleaning. This leads to higher energy consumption, chemical use, and process downtime.
Luckily, there’s an innovative solution for these fouling issues. Altum’s ZPD (Zero Process Downtime) Ultrasound solution offers a chemical-free, efficient method for fouling removal and prevention to increase evaporator uptime. The solution is externally applied, which means the process does not need to be stopped and equipment does not need to be taken apart. By using ultrasound for fouling prevention, no harsh fouling prevention or removal chemicals are needed.
Altum’s high-power ultrasound solution prevents fouling in evaporators, often calcium-based, by inducing a crystallization effect. By sonicating black liquor before it goes through the heated elements in an evaporator, ultrasound can induce nucleation and create a controlled crystallization effect so that the black liquor will not adhere to heated surfaces as scale. See picture below for visual explanation.
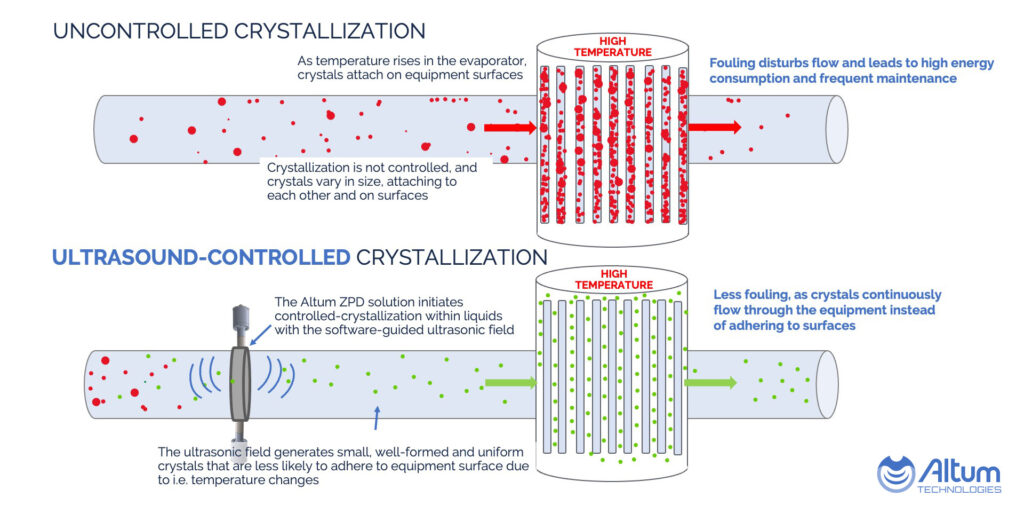
Overall, benefits of using Altum’s ultrasound in evaporators include
- Less production downtime and lost production
- Better energy efficiency
- Lower water & chemical consumption
- Increased operational safety
Next, we’ll take a look at two of our fouling prevention cases in evaporators to highlight how we can improve evaporator uptime.
Case 1: Increasing operation uptime and decreasing acid use at Mitsubishi Paper
This project was done in collaboration with our local partner in Japan, Nippon Steel Engineering Co., Ltd.
This Mitsubishi Paper mill faced challenges with scaling in their black liquor evaporators, mainly due to calcium carbonate buildup. The scale was very hard in texture and was difficult to remove with traditional methods. The mill tried chemical injections, but they proved ineffective in solving the issue.
The scale reduced the efficiency of the heat transfer surface and prevented the black liquor from contacting the heated surface below the deposition area. This made it impossible to secure enough heat transfer area and resulted in both reduced heat transfer efficiency and evaporation efficiency. It also made it difficult to maintain the process, especially for the four-month period during the winter. In the worst case, the process had to be stopped every month for a cleaning break.Additionally, the regulated chemical the mill used to clean the scaling can harm the equipment due to its corrosive tendencies.
Altum’s ultrasound solution was externally applied on the inlet pipe to the evaporators to induce a controlled cystallization effect, preventing the crystals from adhering to the heated surfaces.
The results from this installation were measured by monitoring the difference in temperature between the heating steam and the black liquor in addition to visually inspecting the evaporator when opened. The temperature difference is a crucial metric: once it exceeds 20 °C, the operation is shut down for cleaning. Before ultrasonic treatment, the difference reached 20 °C in approximately a month.
Altum’s ultrasound solution proved highly effective. With ultrasonic treatment, the temperature difference remained constant, enabling stable, continuous operation for four months. In addition to increased evaporator uptime, the evaporator was also visibly cleaner when opened (see pictures below for comparison).
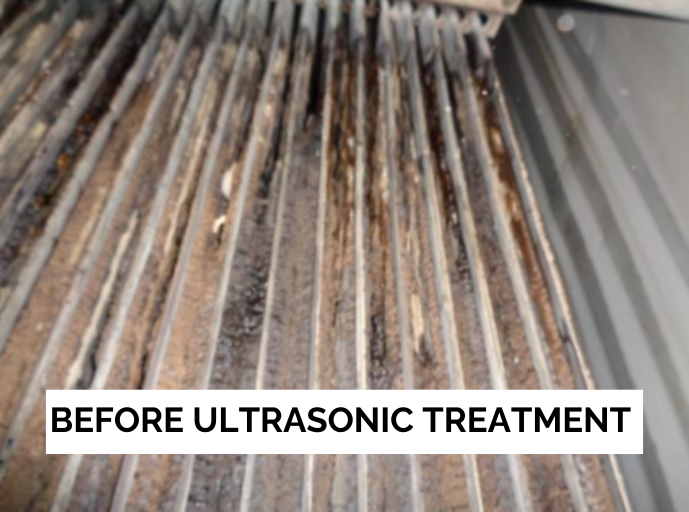
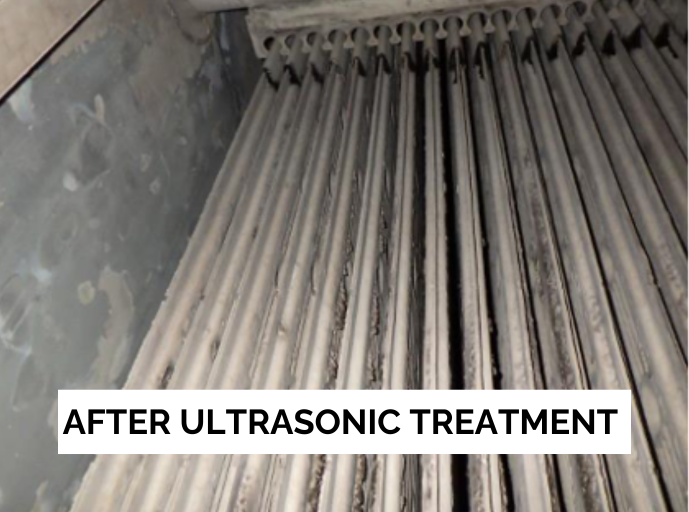
Results achieved:
- 300% increase in operation cycle length (from a month to 4 months).
- Decreased maintenance needs.
- No need for acid use.
- A more stable, predictable & efficient process.
Case 2: Decreasing maintenance needs and improving energy efficiency
In a Finnish Pulp & Paper mill, there were significant fouling issues in two evaporators. There were seven evaporators in series, and during the flow from evaporator 6 in the beginning of the process to the last evaporator 1A, fluid from the process liquid evaporated and the dry material content of the liquor increased from around 10 % to over 50 %. As a side effect of this process, the black liquor flowing through the series of evaporators caused calcium-based fouling issues especially in the hottest evaporators at the end of the series, 1A and 1B.
This fouling in the evaporators reduced energy and process efficiency and frequently reduced total pulp manufacturing capacity. In the worst case, the warmest evaporator (1A) needed two cleaning stops (1-5 days per stop) per month, whereas the 2nd warmest evaporator (1B) needed one cleaning stop per month: this translates to around 120 days of cleaning per year.
Altum’s multichannel solution was installed on the pipes of evaporators 1A and 1B and operated remotely using Altum’s software. To measure the results, we monitored pump current levels and flow rate.
Results achieved:
- Stability of the pump current levels improved.
- Energy efficiency improved by 10% per unit.
- Amount of washes decreased 75% for evaporator 1A and over
85% for evaporator 1B. This means that washes for evaporator 1A were reduced from 8 to 2, and for 1B from 12 to 1-2 per year.
Want to find out how you can reach similar results while making your process more sustainable and environmentally friendly? Don’t hesitate to contact our experts for more information on increasing evaporator uptime!
Follow us on LinkedIn to stay tuned for our future news and insights.