Extensive maintenance activities and process disruptions due to fouling are a nuisance in many industries. Struvite fouling is a persistent issue in the biogas industry, resulting from the presence of magnesium, ammonium, and phosphate during the anaerobic conditions integral to the biogas production process. This buildup can then significantly hinder operations by causing clogging in pipes, pumps, and heat exchangers.
Struvite fouling posed a challenge for our customer Ductor, which encountered fouling across various stages of its process. In this blog post, we’ll discuss how Altum’s ZPD (Zero Process Downtime) ultrasound solution helped solve these challenges: what did we do, why and how, and what did we achieve?
Objective:
Ductor builds, owns, and operates microbiological turnkey facilities, turning waste from the agricultural sector into sustainable fertilizers and biogas. This facility produces biogas from manure while recovering material for organic liquid nitrogen fertilizer.
Due to the struvite fouling in the pipelines, plate and frame heat exchangers and pumps, cleaning had to be performed every one to two days and was done with CIP (Clean-in-place) using citric acid and high-pressure wash. This in turn led to production downtime, manual labor, and the handling of chemicals.
The objective was to significantly increase production uptime by preventing buildup in equipment.
Solution:
Altum’s ZPD ultrasound solution was externally installed on the pipelines to prevent fouling. When preventing struvite fouling, Altum’s solution works by creating an ultrasonic field in the equipment which prevents the foulant from attaching to the surfaces. With Altum’s solution, this field is created with precision and is software-guided to ensure control and the best possible results.
Results:
The results from this installation were measured in process uptime and lowered need for maintenance. So far, Altum’s solution has been able to keep the process clean for 8 weeks. By implementing Altum’s solution, the customer has been able to reduce process downtime associated with cleaning from 2 hours per day to just 2 hours per month. On top of this, the process has become much more stable, and the biogas production and biological fertilizer recovery processes have been improved.
Overall, with Altum’s solution:
- Decrease in operation downtime, from 2 hours/day to 2 hours/month.
- 6 tons decrease in citric acid use per year.
- Reduced CO2 emissions.
- An improved and stable production and recovery process.
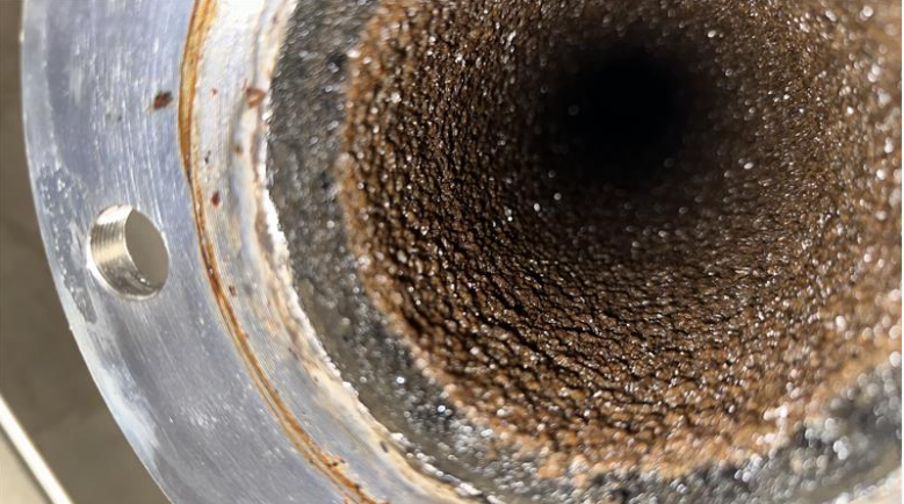
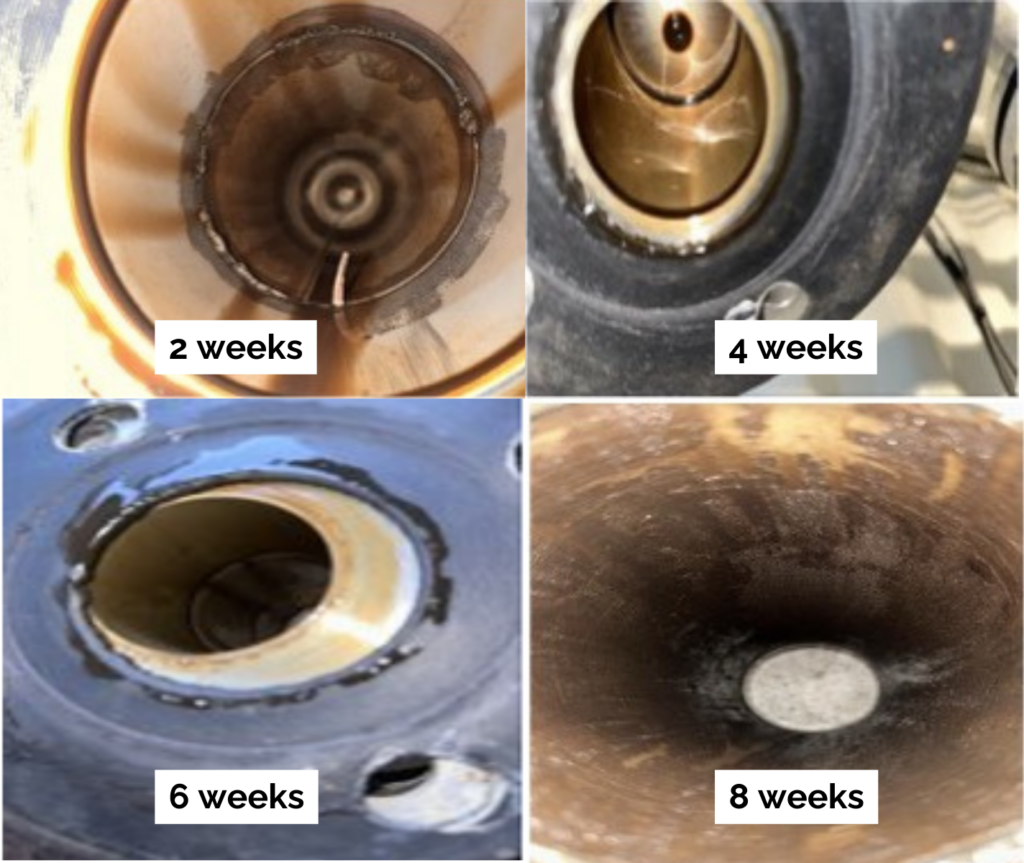
Before: thick buildup of struvite (10 mm) on pipes.
After: very minimal buildup after 8 weeks of production.
With Altum’s solution, we have been able to substantially increase our operation uptime and decrease maintenance needs and the use of chemicals. Collaboration has been easy, and we are very happy with Altum’s services!
Miitrei Yli-Puntari, Ductor
Want to find out how you can reach similar results while making your process more sustainable and environmentally friendly? Don’t hesitate to contact us!
Remember to follow us on LinkedIn to stay tuned for our upcoming updates and insights.