This project was done with Altum Technologies’ local partner in Japan, Nippon Steel Engineering Co., Ltd.
Black liquor evaporation is a vital process in kraft pulping: plants can produce energy from black liquor, enabling self-sufficiency in energy needs and use. In the best-case scenario, energy produced from black liquor can also be sold locally through a district power grid and can thus be an important source of revenue. The efficiency with which the mill can evaporate and concentrate diluted black liquor directly impacts its ability to generate energy efficiently in recovery boilers. However, scaling and fouling pose a significant challenge, as black liquor has been observed to adhere as calcium carbonate scale on heated surfaces in evaporators. This leads to increased use of chemicals due to removal attempts, frequent cleaning stops, and overall decrease in the whole evaporation process efficiency.
In this blog post we will discuss results we’ve achieved with our solution installed on a black liquor evaporator for fouling prevention at one of Mitsubishi Paper’s mills. What did we do, why, and what did we achieve?
Objective: Decreasing maintenance needs and increasing efficiency
This Mitsubishi Paper mill had been experiencing issues with scaling in black liquor evaporators, mainly caused by calcium carbonate. The scale formed in this process is very hard in texture and difficult to remove. As a potential solution, the mill tried chemical injections, but this just led to the scale shifting downstream and becoming a problem at the second effect evaporator. The scale itself not only reduced the efficiency of the heat transfer surface, but also prevented the black liquor from contacting with the heated surface below the area where it is deposited, making it impossible to secure enough heat transfer area. This resulted in both reduced heat transfer efficiency and evaporation efficiency.
Due to these scaling issues, it became difficult to maintain the process, especially for the intended four-month period during the winter. In the worst case, the process had to be stopped every month for a cleaning break. On top of this, the chemical this mill used to try and clean the scaling is regulated and can be harmful to the equipment due to its corrosive tendencies. Thus, this mill wanted to try out Altum’s ZPD Ultrasound solution to prevent the scaling altogether.
Solution: Fouling prevention through crystallization
Altum’s multichannel ZPD (Zero Process Downtime) solution was installed on the inlet pipe to the evaporators. When preventing scaling in black liquor evaporators, Altum’s solution works by inducing a crystallization effect. By sonicating black liquor before it goes through the heated elements in an evaporator, ultrasound can induce nucleation and create a crystallization effect so that the black liquor will not adhere to heated surfaces as scale.
With Altum’s solution, the intensity of the ultrasonic waves is powerful enough so that the crystallization effect occurs even in viscous liquids such as black liquor. Our solution is installed externally, so there is no need to dismantle equipment or stop production.
Results:
The results from this installation were measured both by monitoring the difference in temperature between the heating steam and the black liquor and by visually inspecting the evaporator when opened. The difference in temperature forms an important metric, as once it exceeds 20 °C the operation is seen as no longer operational and is shut down for cleaning.
Before ultrasonic treatment, the temperature difference reached 20°C within approximately a month. However, with ultrasonic treatment, it remained constant, enabling stable, continuous operation for four months. Additionally, upon opening the evaporator after sonication, it was visibly cleaner (see pictures below for comparison). Scaling was prevented to the extent that hydrochloric acid cleaning, which was previously required during regular maintenance breaks, was no longer necessary. Furthermore, no chemical injections were needed during the long winter operation cycle.
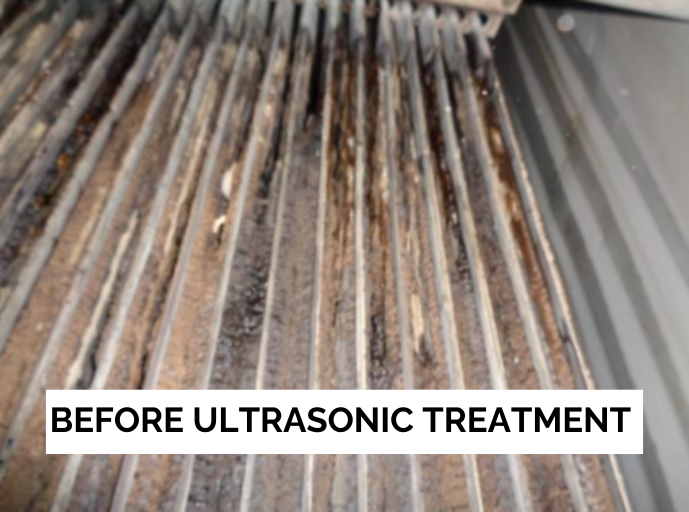
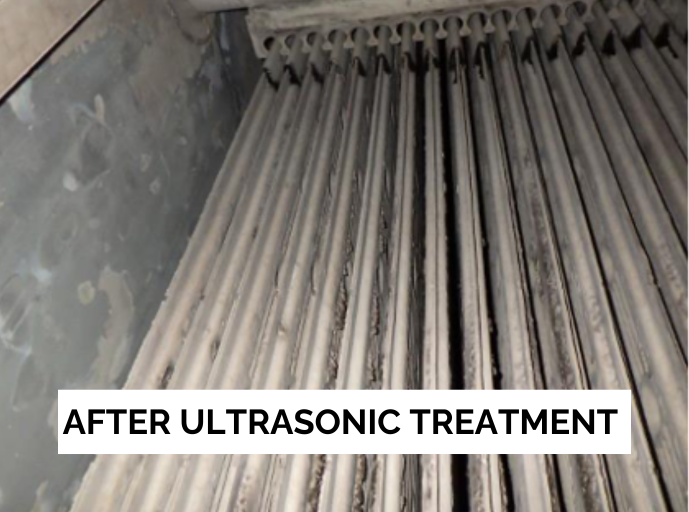
Overall, with Altum’s solution:
- 3 months longer operation cycle (from a month to 4 months).
- Decreased maintenance needs.
- No need for acid use.
- A more stable, predictable & efficient process.
Want to find out how you can reach similar results while making your process more sustainable and environmentally friendly? Don’t hesitate to contact us!
Remember to follow us on LinkedIn to stay tuned for our upcoming updates and insights.
This blog post is based on the white paper done by Mitsubishi Paper, published in conjunction with the TAPPI Japan technical seminar held in October 2023.