Pulp & Paper
Case:
FOULING PREVENTION IN A BLACK LIQUOR HEATER
ASIAN P&P COMPANY | ASIA
By preventing fouling in a black liquor heater, extra steam was no longer necessary and flow rate was improved.
ISSUE
Fouling disrupted the black liquor evaporation process and led to decrease in production efficiency and output, as well as increase in energy consumption.
- The temperature of the black liquor after the heater needs to be at least 150 °C to maintain an efficient production process, however, the temperature was difficult to maintain due to the decrease in heat transfer efficiency caused by fouling.
- As fouling increased, more steam was required to be fed into the pipe to maintain production efficiency, resulting in a higher energy demand.
- Scaling issues in the black liquor heater was a major bottle neck in maintaining process efficiency.
- Decrease in the flow rate of liquid was a clear sign of fouling.
Without a properly functioning heater the whole process stops.
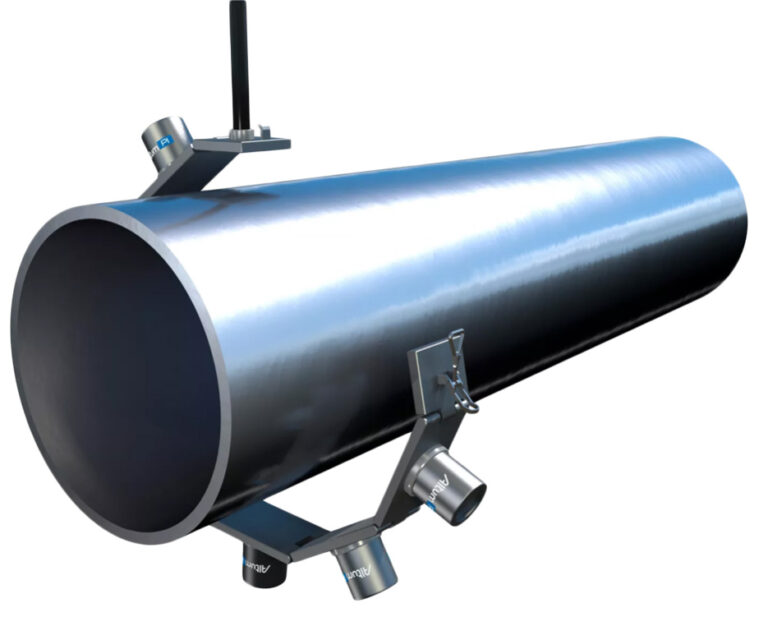
SOLUTION
Multichannel solution installed with multiple COD (Clamp-On Device) belts.
The transducers were attached to the inlet pipe upstream to the heater to induce sonocrystallization effect as a fouling prevention method. Sonocrystallization effect controls the crystallization in the liquid to avoid crystals attaching on equipment surfaces.
RESULTS
- More stable flow rate and overall improvement of flow rate over 5 %.
- While sonication was on, temperature stayed stable and stayed around 150 °C. When sonication was stopped, temperature could not be kept at 150 °C.
- Steam valve opening degree remained below 80% during sonication for over 8 weeks, meaning no extra steam was required to maintain original production efficiency – without sonication the opening degree reached 100% in 4 weeks.