Mining & Minerals
Case:
PREVENTING FOULING IN A CRYSTALLIZER
MINERALS PROCESSING COMPANY | FINLAND
By preventing fouling in a nickel sulfate crystallizer, operation cycle duration was increased by 100%.
ISSUE
The issue in this particular case was a common one: due to scaling issues in a DTB crystallizer, the process had to be stopped every five days to wash the crystallizer with hot water. This process took approximately one day per stoppage, leading up to over 70 days of lost production annually. The crystallizer formed a clear bottleneck in the process: when it was not able to receive the process liquid, it had to be fed back to the previous process stage. If the crystallizer was out of order due to, for example, a washing period or reduced capacity caused by fouling, some tonnages were even lost completely. The goal was to lengthen the production cycle and reduce maintenance stops by preventing scaling.
70+ DAYS
OF LOST PRODUCTION ANNUALLY
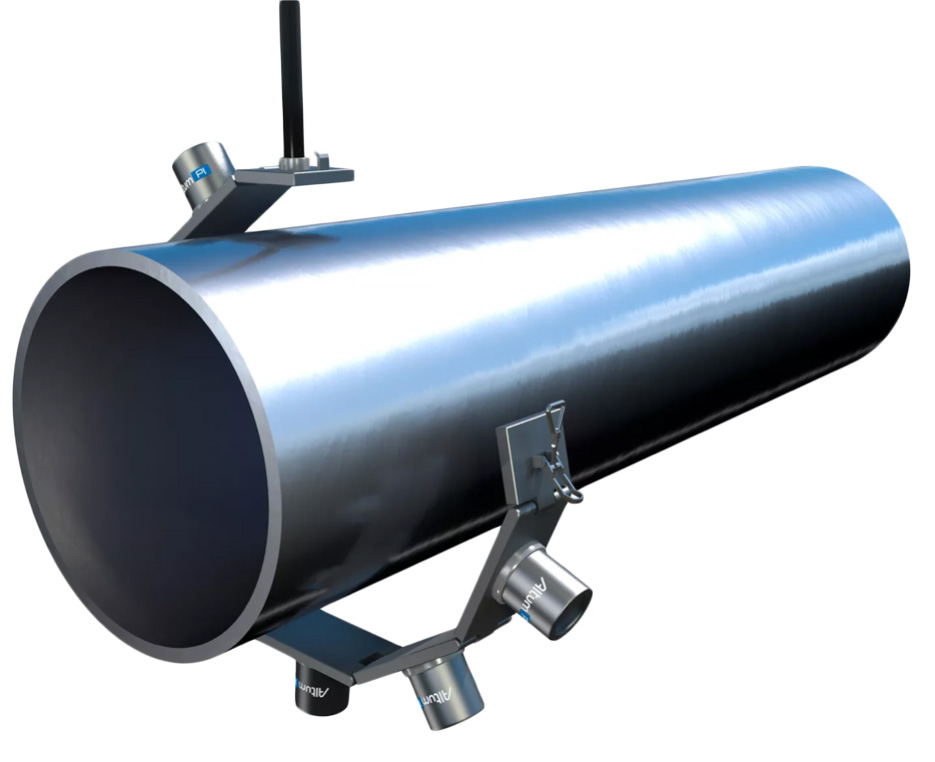
SOLUTION
In this case:
- Multichannel solution attached on crystallizer.
- Ultrasound creates microscopic vibrations on the inner surface of the equipment to prevent or detach the foulant.
- Sonication done with alternating power and multiple channels to ensure an even ultrasonic field and vibration.
RESULTS
- Time between maintenance breaks increased by 100%, from 5 to 10 days.
- The added ∼35 days of uptime increase end product production by 1100 tons a year, leading to increased profits.
- Increased energy and operational efficiency: Clean equipment consumes less energy, allowing the process to operate optimally.
BENEFITS OF ALTUM'S SOLUTION