Pulp & Paper
Case:
FOULING PREVENTION IN EVAPORATORS
FINNISH P&P COMPANY | FINLAND
By preventing fouling with Altum's ultrasound, this Finnish pulp & paper mill was able to create substantial improvement in process efficiency and lower energy consumption and cost.
ISSUE
At this facility, there were seven evaporators in series, and during the flow from evaporator 6 in the beginning of the process to the last evaporator 1A, fluid from the process liquid evaporated and the dry material content of the liquor increased from around 10 % to over 50 %. As a side effect of this process, the black liquor flowing through the series of evaporators caused calcium-based fouling issues especially in the evaporators at the end of the series, 1A and 1B.
- Fouling in the black liquor evaporators reduced energy and process efficiency and frequently reduced total pulp manufacturing capacity.
- In the worst case, the warmest evaporator (1A) needed two cleaning stops (1-5 days per stop) per month, whereas the 2nd warmest evaporator (1B) needed one cleaning stop per month.
- Constant “firefighting” and disturbance caused by the need to clean evaporators 120/365 days a year.
UP TO 120 DAYS PER YEAR
OF PRODUCTION INTERRUPTIONS
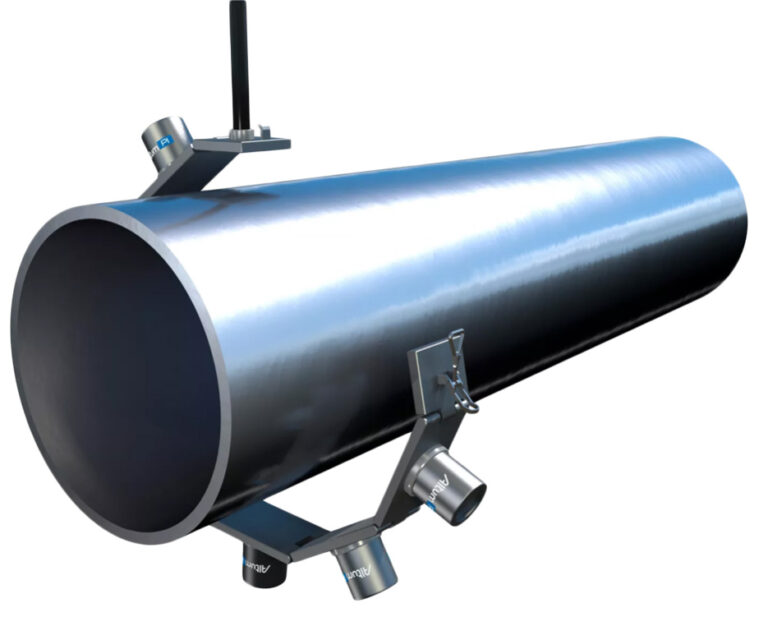
SOLUTION
A multi-channel solution was placed on the pipes of evaporators 1A
and 1B to create an even ultrasonic field.
- Multi-channel solution
- Remote operation of the transducers with Altum's software
RESULTS
Pump current levels and flow rate were measured to see the effect of Altum's solution:
- Pump current levels became more even and stable.
- Energy efficiency improved by 10% per unit.
- Amount of washes decreased 75% for evaporator 1A and over
85% for evaporator 1B.